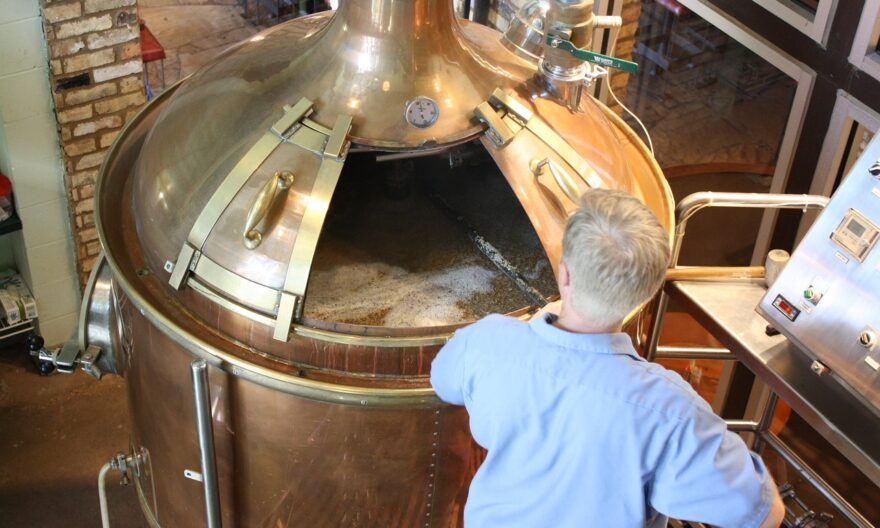
Rola konstrukcji i parametrów roboczych w jakości przemiału i rozproszenia
W nowoczesnych liniach technologicznych, gdzie istotne jest szybkie i dokładne mieszanie składników o różnych właściwościach fizykochemicznych, kluczowe znaczenie ma wybór odpowiednich urządzeń mieszających. Szczególnie w przemyśle chemicznym, kosmetycznym, farbiarskim czy spożywczym, jakość procesu zależy od efektywności rozdrabniania, homogenizacji oraz dyspersji komponentów. W tym kontekście niezwykle ważną funkcję pełni disolwer – urządzenie wysokoobrotowe, które znajduje zastosowanie wszędzie tam, gdzie wymagane jest precyzyjne i powtarzalne mieszanie materiałów ciekłych z ciałami stałymi lub półstałymi.
Disolwer działa w oparciu o zasadę szybkiego obrotu specjalnie ukształtowanego mieszadła tarczowego, które generuje intensywne zawirowania i siły ścinające, umożliwiające skuteczne rozbijanie aglomeratów cząstek oraz ich równomierne rozproszenie w cieczy. Dzięki temu proces mieszania jest znacznie bardziej efektywny niż w przypadku konwencjonalnych mieszadeł mechanicznych. Wysoka prędkość obrotowa oraz odpowiedni dobór geometrii narzędzi mieszających pozwalają na uzyskanie jednolitej konsystencji nawet w przypadku substancji o dużej lepkości.
Zaletą, jaką charakteryzuje się disolwer, jest możliwość dostosowania parametrów pracy – takich jak prędkość obrotowa, czas cyklu czy pozycjonowanie mieszadła – do konkretnego typu surowca i pożądanego efektu końcowego. Nowoczesne konstrukcje wyposażone są często w falowniki, czujniki momentu obrotowego oraz systemy pomiarowe kontrolujące temperaturę, lepkość i gęstość medium. Tego typu zaawansowanie technologiczne przekłada się na powtarzalność partii produkcyjnych oraz lepszą kontrolę jakości.
Optymalizacja procesów i zastosowanie w środowiskach o wysokich wymaganiach technicznych
Wybór disolwera jako elementu wyposażenia linii produkcyjnej przynosi korzyści nie tylko w zakresie efektywności operacyjnej, ale również bezpieczeństwa i ergonomii pracy. Konstrukcje tych urządzeń projektowane są z myślą o łatwym czyszczeniu, odporności na agresywne media i spełnianiu norm sanitarnych. W przemyśle farmaceutycznym i kosmetycznym wykorzystywane są modele ze stali nierdzewnej z certyfikatami zgodności z normami GMP i FDA.
Disolwer może pracować w trybie wsadowym lub ciągłym, w zależności od potrzeb danej aplikacji. Istnieją również wersje laboratoryjne, które pozwalają na precyzyjne testowanie receptur przed ich wdrożeniem na skalę przemysłową. Dzięki temu możliwe jest nie tylko skrócenie czasu wprowadzenia produktu na rynek, ale również ograniczenie strat materiałowych i energetycznych. W wielu zakładach przemysłowych disolwer stanowi serce procesu technologicznego, od którego zależy jakość finalnego wyrobu.
Szczególnym wyzwaniem w przypadku materiałów trudnorozpuszczalnych lub o tendencji do sedymentacji jest utrzymanie stabilności mieszaniny przez cały czas procesu. Tu również disolwer sprawdza się dzięki zdolności do generowania intensywnego przepływu turbulentnego, który zapobiega opadaniu cząstek stałych i wspiera ich trwałe zawieszenie w cieczy. Odpowiednio zaprojektowana geometria zbiornika, układ mieszadła i charakterystyka napędu stanowią o skuteczności działania i niskim zużyciu energii.
Podsumowując, disolwer to urządzenie o kluczowym znaczeniu dla wielu branż przetwórczych. Jego zastosowanie umożliwia osiągnięcie wysokiej jakości produktów przy jednoczesnym zachowaniu wydajności i powtarzalności procesów. Nowoczesne rozwiązania konstrukcyjne, zaawansowane systemy sterowania oraz szeroka gama zastosowań czynią z disolwera niezastąpiony element wyposażenia zakładów produkcyjnych, w których jakość rozproszenia i jednorodność mieszanin są kluczowe dla sukcesu rynkowego produktu.