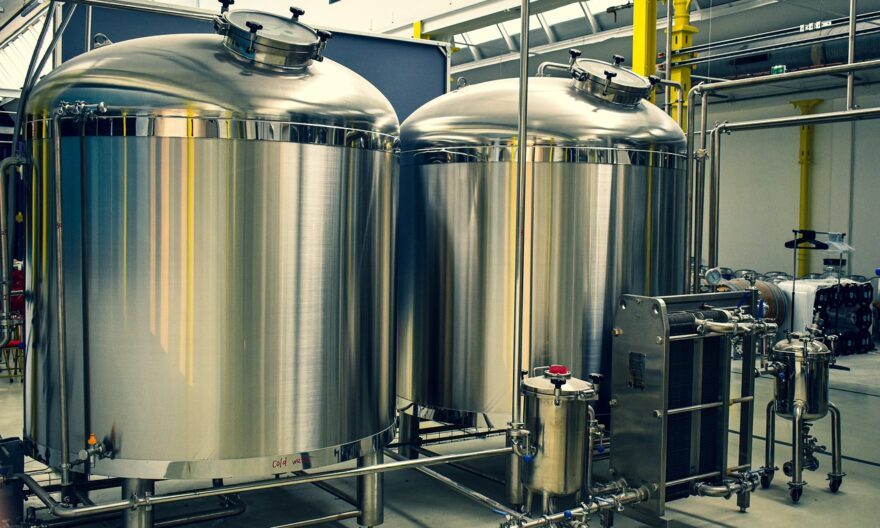
Kluczowe parametry technologiczne i znaczenie w procesach dyspersji
W wielu gałęziach przemysłu, od chemii po kosmetykę i produkcję farb, niezwykle istotnym elementem procesu technologicznego jest skuteczne łączenie składników o zróżnicowanych właściwościach fizycznych. Tam, gdzie wymagana jest wysoka jednorodność mieszaniny i precyzyjne rozdrobnienie cząstek stałych w cieczy, stosuje się specjalistyczne urządzenia wysokoobrotowe. Jednym z najczęściej wykorzystywanych rozwiązań tego typu jest disolwer – maszyna przystosowana do intensywnej pracy w warunkach przemysłowych, gwarantująca powtarzalność i efektywność operacyjną.
Disolwer to mieszadło talerzowe z napędem o regulowanej prędkości, które generuje silne siły ścinające, odpowiedzialne za rozbijanie cząstek stałych i ich równomierne rozprowadzenie w ośrodku ciekłym. Urządzenie to wykazuje szczególną skuteczność przy mieszaniu substancji o dużej lepkości, gdzie tradycyjne mieszadła zawodzą. Zastosowanie disolwera pozwala nie tylko na przyspieszenie procesu, ale także na uzyskanie stabilnej, nieulegającej sedymentacji mieszaniny, co ma znaczenie np. przy produkcji past, emulsji czy lakierów.
Na rynku dostępne są różne konfiguracje disolwerów – od modeli laboratoryjnych, umożliwiających testowanie nowych receptur, po wersje przemysłowe o pojemności zbiorników sięgającej kilku tysięcy litrów. Kluczowym elementem przy wyborze urządzenia jest dostosowanie jego parametrów do rodzaju surowców i wymagań procesu. Prędkość obrotowa, geometria tarczy, głębokość zanurzenia, a także możliwość regulacji – to czynniki wpływające na skuteczność działania. W nowoczesnych liniach produkcyjnych disolwer może być również zintegrowany z systemami automatycznego dozowania, rejestrowania parametrów procesu i kontrolą jakości online.
Przewagi procesowe i kryteria wyboru urządzenia w kontekście branżowym
Efektywność pracy urządzenia zależy nie tylko od jego mocy i konstrukcji, ale także od jakości wykonania i zgodności z normami sanitarnymi oraz bezpieczeństwa. W przemyśle kosmetycznym czy farmaceutycznym stosuje się disolwery wykonane ze stali nierdzewnej, zgodne z wytycznymi GMP. Ważna jest również łatwość czyszczenia, możliwość pracy w systemie CIP oraz konstrukcja eliminująca strefy martwe, które mogłyby prowadzić do zanieczyszczenia produktu końcowego. Z kolei w przemyśle farbiarskim, klejowym czy przy produkcji tynków cienkowarstwowych, istotna jest wytrzymałość na intensywne obciążenia mechaniczne i odporność na substancje agresywne chemicznie.
Disolwer może być wyposażony w dodatkowe elementy, takie jak zbiorniki z płaszczem grzewczym, systemy podciśnieniowe czy mieszadła pomocnicze. Wszystkie te rozwiązania zwiększają kontrolę nad przebiegiem procesu i pozwalają na dostosowanie technologii do indywidualnych wymagań produkcyjnych. Dużą zaletą tego typu urządzeń jest również ich uniwersalność – jeden disolwer może być stosowany w różnych recepturach, co znacząco wpływa na ekonomikę produkcji i skraca czas przezbrojeń.
W procesach, gdzie liczy się jednocześnie szybkość, jakość i powtarzalność, disolwer pozostaje jednym z najbardziej niezawodnych narzędzi do przygotowania mas i zawiesin. Jego zastosowanie pozwala na poprawę efektywności energetycznej, zmniejszenie strat surowcowych oraz lepsze wykorzystanie przestrzeni produkcyjnej dzięki kompaktowej budowie. Co więcej, zastosowanie automatyki procesowej umożliwia integrację urządzenia z systemami zarządzania produkcją (MES), co wspiera realizację standardów Przemysłu 4.0.
Podsumowując, disolwer to zaawansowane technologicznie urządzenie, które znajduje zastosowanie w wielu branżach przemysłu przetwórczego. Odpowiedni dobór modelu i parametrów pracy pozwala nie tylko zwiększyć jakość i stabilność produktów, ale również zoptymalizować koszty operacyjne i podnieść efektywność całego procesu. W środowisku wymagającym precyzyjnej kontroli nad każdym etapem produkcji, disolwer pozostaje nieocenionym narzędziem wspierającym innowacyjność i konkurencyjność przedsiębiorstw.